CUSTOMER STORY
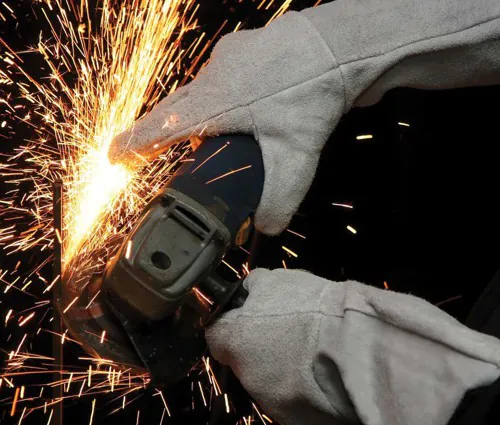
As our business grows and we outgrow our current capacity we will certainly purchase another Pathfinder because the quality, service and value are unmatched elsewhere in the market.
Southern Gloves expands with multiple Pathfinder cutters
Southern Glove is a manufacturer of industrial work gloves and safety product which we cut and assemble in Honduras. To cut our product component parts, we used old presses previously used in the automotive industry to stamp out automotive body parts. This cutting process required dies which were very costly to purchase and maintain. If we needed to change a pattern to make a new glove it required an investment of over $30,000 in new dies plus we were limited to using narrow fabric which capped the potential of increasing our material yields.
After a thorough analysis of the cutting technologies available at the time, Southern Glove purchased its first Pathfinder cutting machine in October 2008. The initial installation in Honduras went very smoothly and we were up and running within a day after the machine was delivered. Our operators were trained within two weeks.
Our factory in Honduras where the machine was installed is not climate controlled so the Pathfinder is operating in temperatures in excess of 100°F or 38°C and an average relative humidity of more than 80%. Also the reliability and consistency of the power supply is very spotty in Honduras resulting in many brownouts and blackouts. Considering these extreme conditions the machine has performed extremely well with minimal downtime due to these conditions.
After perfecting our patterns, cut files and solving our operations issues we have realized an increase in yield of over six percent and an annual material savings of over $100,000. Now we are able to change patterns on the fly and offer our customers more value added service in the form of customized products that our competitors cannot match. The financial benefit and competitive advantage gain provided by the Pathfinder prompted us to purchase another machine in 2010. We operate the machine over 100 hours per week.